Case PepsiCo - Mathura (India)
ASRS with Multi - Pro shuttle solution and sortation
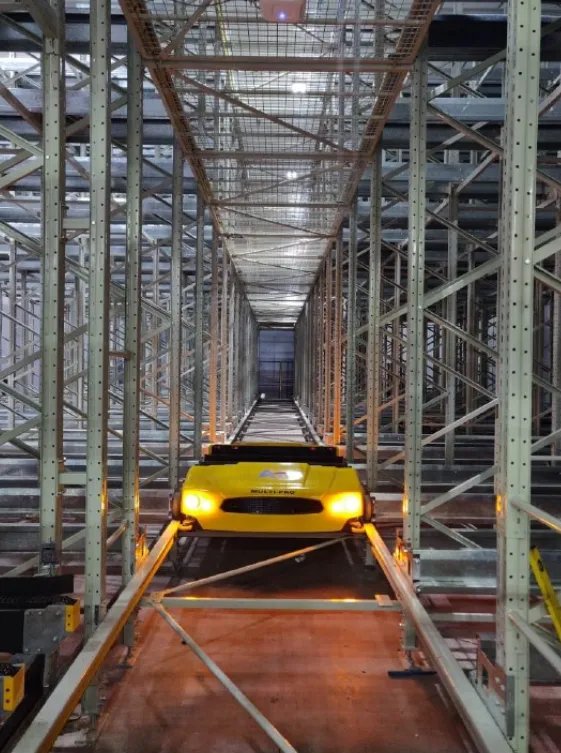
PepsiCo wanted to set up their 4th production plant in India, which is also their largest plant & it is with a captive warehouse.
This being the largest plant and due to the storage and throughput issues they have been facing with the other 3 largely manually operated plants, they decided to go for a fully automated facility.
As part of that, they approached us for the automation of their warehouse.
Given the scale of the project, we decided to do it in 2 phases, where in, in Phase-1 we automated the Low Bay Area which deals with the storage of Lays, Doritos, Uncle chips and Quaker oats. Here, we weaved a solution around our mother-child ASRS.
Phase 2 gone live in 2023: we proposed a stacker crane based ASRS for the storage of the rest of the brands of Pepsi.
PepsiCo is an American multinational food, snack, and beverage corporation. PepsiCo’s business encompasses all aspects of the food and beverage market.
Business Case
Background: This PepsiCo plant in India is the largest one in regard of storage and throughput and therefore the decision was made to go for a fully automated facility.
Objective: The operation should have a storage system with the capability to receive, store, pick full pallet products. Pallets will be received into the warehouse via an automated solution from a production pickup location and from trucks via the loading docks.
Storage and Materials Handling:
Storage system consists of G+4 levels with 3440 pallet storage locations
3 infeed lines to the storage section (2 from the plant and 1 from vendors) and 2 outfeed lines
4Multi-Pro (multi-deep) for the upper 4 levels of storage
Order sortation happens at the ‘G’ level: 1 mother shuttle acting as a transfer cart to the 6 single deep Mother Child shuttle systems.
In total, 11 Mother shuttles and 10 Child shuttles with other supporting systems
Throughput: 135 pallets/hour (pallets from production and from Inbound),Outbound throughput is 160 pallets/hour with 2 outfeed units
Software and Controls
Optimus,our WMS is used to control and maintain the entire operation and provides traceability by batch and handling unit.
Benefits
High Operating speed and throughput
WCS ensures traceability and provides the capability to allocate product on a prioritized bases given by a set of rules established by PepsiCo.
Results:
With an Inbound throughput of 86 pallets/hour from the production plant & 35 pallets/hour from the outside vendors, togethher the solution has a capacity to process 135 pallets/hour.
Also from the 2 outfeed units, the outboud throughput is 160 pallets/hour.
Direct integration between SAP EWM, WMS & PLC eliminates need of any middleware this makes the system easy to maintain and troubleshoot.
Same system (Multi-pro) used for order sortation & storage creates a seamles flow of information b/n the 2 operations that’ sresulting in higher accuracies & throughputs at the last touch point of warehouse operations.
In continuation – We are implementing the phase – 2 project (Hihg Base Area) that through mezzanine tot he Low Base Area (phase-1 project).