Bus Industrial Tools gaat voor stapsgewijze centralisatie
Doordachte magazijninrichting biedt steun bij bundelen logistieke activiteiten
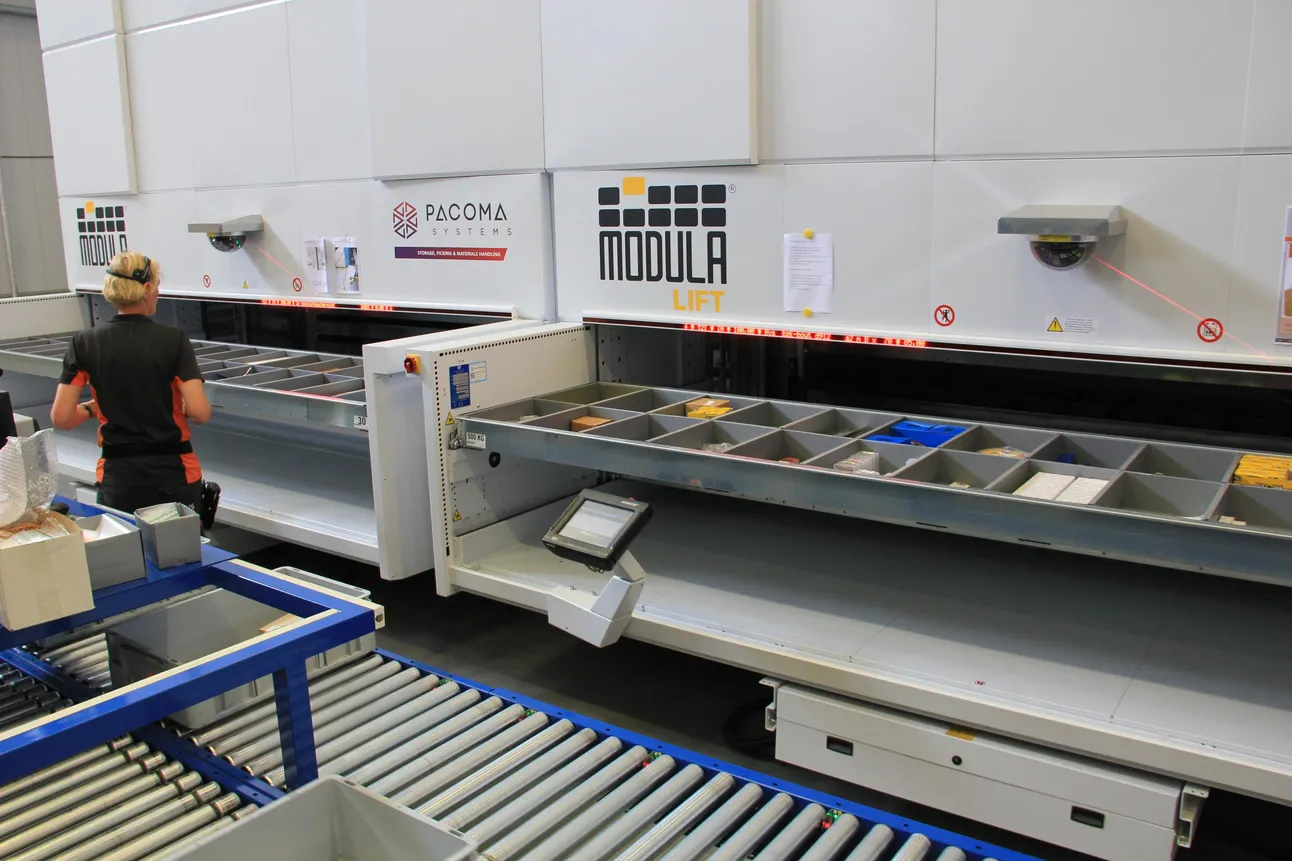
Om zijn logistieke efficiëntie te verhogen, besloot het Nederlandse Bus Industrial Tools zijn magazijnoperaties te centraliseren. Voor de organisatie was dat een grote uitdaging, aangezien geen enkele van de tien vestigingen al over een volwaardig logistiek centrum beschikte. De oprichting van het kersverse Landelijk Logistiek Centrum in Zwolle betekende voor het bedrijf dan ook het begin van een logistieke transformatie. Binnen de nieuwe structuur speelt een uitgekiende combinatie van verticale liftsystemen en legbordstellingen voor de opslag en conveyors voor het intern transport een sleutelrol. Daarbij sloegen Pacoma Systems en Vanas Engineering de handen in elkaar.
Bus Industrial Tools werd in 1957 opgericht als groothandel in gereedschappen. Vandaag profileert het bedrijf zich als totaalleverancier voor de on/offshore metaal- en industriesector. Het bedrijf levert niet alleen producten, zoals een waaier aan gereedschappen en tools op het vlak van las- en snijtechniek, maar is ook een toegewijde partner bij de realisatie van kwalitatieve technische oplossingen. Maatwerk maakt hier onlosmakelijk deel van uit. Die strategie onderscheidt Bus Industrial Tools meteen ook van distributeurs pur sang.
Erik Gies, manager Operations bij Bus Industrial Tools: “Om onze klanten optimaal te bedienen, hebben wij vestigingen in Nederland en ook een in het VK. Naast ons algemene aanbod biedt onze organisatie specifieke diensten zoals reparaties, keuringen en het beheer van gereedschappen voor klanten. We kunnen gerust stellen dat we in de loop der jaren zijn uitgegroeid tot kennisinstituut op technisch vlak. Aangezien we binnen onze strategie geloven in de kracht van onze tien lokale vestigingen, willen we die behouden om een optimale service te kunnen verlenen.”
Logistiek centrum van scratch
Wel zag Bus Industrial Tools een opportuniteit in het centraliseren van de magazijnactiviteiten. Het assortiment dat de firma kan leveren, is enorm. Over de verschillende vestigingen liggen zo’n 55.000 artikelen op voorraad. Dat aantal naar beneden halen, is een van de strategische doelstellingen.
Om enerzijds de voorraad te optimaliseren en anderzijds de logistieke efficiëntie te verhogen, werd een vijftal jaar geleden beslist om een centraal distributiecentrum in het leven te roepen. Als meest geschikte locatie kwam Zwolle uit de bus, waar de organisatie al zijn hoofdkantoor en een verkoopkantoor heeft en waar voldoende ruimte was om het distributiecentrum te realiseren. Bovendien is het vanop die locatie mogelijk klanten in het hele land snel te beleveren.
E. Gies: “Het gebruik van een centraal logistiek centrum maakt de gemiddelde leverafstand tot onze klanten weliswaar groter, maar het feit dat een efficiënt centraal LC ons toelaat om snel te schakelen compenseert dat ruimschoots. In de lokale vestigingen verliep de orderverzameling trouwens nog zeer manueel via pickbonnen. Er werden ook geen voorraden gealloceerd, wat soms tot vervelende situaties leidde.”
Het landelijke distributiecentrum heeft een vloeroppervlakte van 2.500 vierkante meter. Orders die tot vier uur ’s middags worden geplaatst, krijgt de klant de volgende dag. Naast de reguliere orders zijn er ook spoedorders – bijvoorbeeld voor klanten die aan de balie in Zwolle wachten – die voorrang krijgen. Er wordt in twee shifts gewerkt, met een overlap tussen beide.
Voor de inrichting van het magazijn zat Bus Industrial Tools samen met material handling leverancier Pacoma Systems.
E. Gies: “Onze toenmalige logistieke manager had positieve ervaringen met dat bedrijf. We hebben weliswaar nog een paar andere partijen gecontacteerd, maar zij konden ons geen overtuigend totaalconcept aanbieden. Voor de opslag en picking van een groot deel van onze producten stelde Pacoma Systems ons de Modula-liften van hun partner Vanas Engineering voor (nvdr: begin april 2019 heeft Vanas Engineering Pacoma Systems overgenomen). We zagen in hen ook partners die op de langere termijn met ons kon meedenken, wat binnen onze bedrijfsfilosofie erg belangrijk is.”
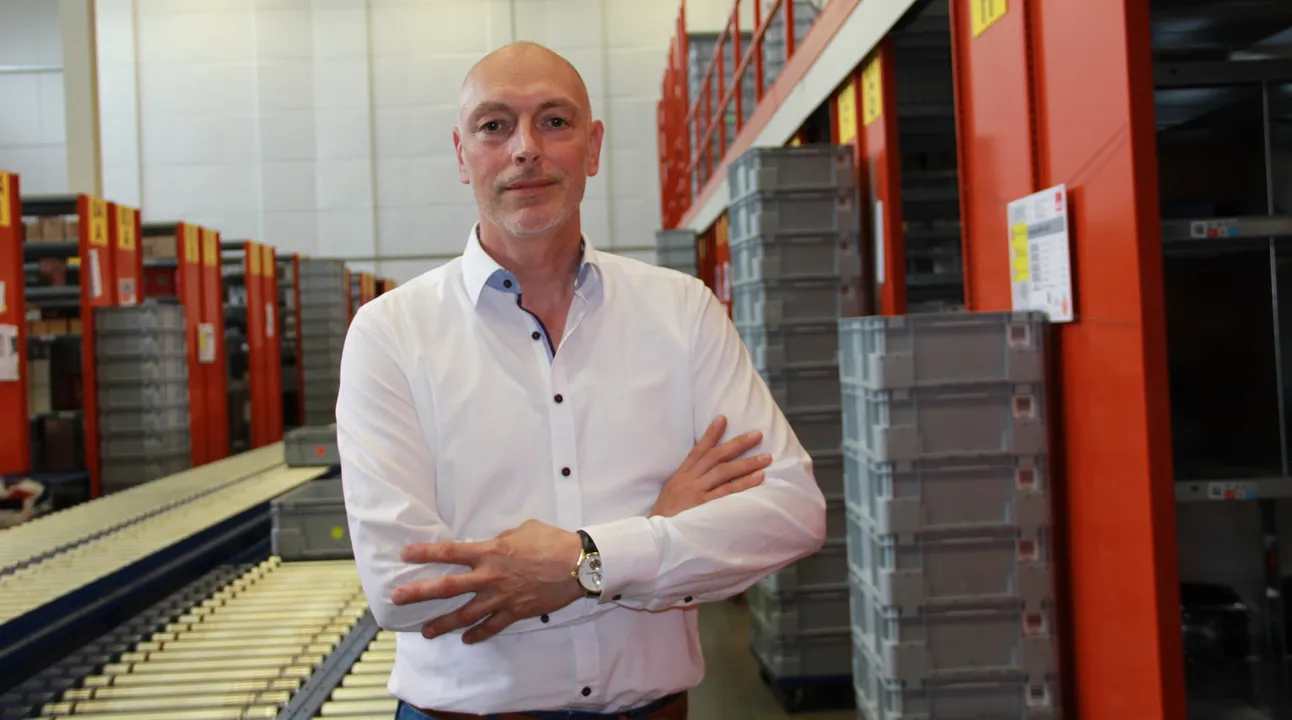
Combo van verticale liftsystemen en conveyors
Alle artikelen met een beperkt formaat – en dat zijn er erg veel – krijgen in het nieuwe logistiek centrum ofwel een plaats in de legbordstellingen ofwel in de vier verticale liftsystemen van Modula, waaraan in totaal twee medewerkers kunnen picken. Er werd gekozen voor ruim 10 meter hoge kasten van 4.100mm breed en 4.058mm diep, omdat die het hoogste rendement per vierkante meter bieden. Elke lade is in compartimenten met verschillende groottes ingedeeld, waardoor de beschikbare ruimte optimaal wordt benut. In totaal vinden we in de liften zo’n 20.000 locaties terug met een enorme diversiteit aan producten. Ruim 70% van de artikelen met een beperkt formaat krijgt een plaats in de lift. Naast de liften en de legbordstellingen heeft Bus Industrial Tools ook een zone met bulklocaties en een voor chemische goederen, zoals oliën, vetten en lijmen.
“Ons nieuwe warehouse management system, MEP (Metric) van Actemium, bepaalt op een dynamische manier of goederen in de liften of op de legborden terechtkomen. Daarbij speelt vooral de dimensie van de producten een rol”, licht Erik Gies toe. “Nieuwe producten meten we dan ook altijd eerst en vervolgens bepaalt een medewerker met een goed ruimtelijk inzicht hoeveel van die items er op een locatie kunnen. De omloopsnelheid speelt bij de plaatsbepaling minder een rol. Doordat we zoveel specials leveren hebben we trouwens maar weinig ‘fast movers’.”
Voordeel van de Modula-liften is dat op een beperkte oppervlakte heel veel goederen kunnen worden opgeslagen. “Dankzij de Modula-liften kunnen we ook snel werken”, getuigt Erik Gies. “Door de externe werkopening kan het systeem al een tweede lade klaarzetten terwijl de medewerker nog aan het picken is. Zo kunnen we vlug van lade wisselen. Ook de aansturing van de Modula-liften via de slimme software Gigasoft.Extended draagt bij tot de hoge efficiëntie. Die software – ontwikkeld door Vanas Engineering – is gekoppeld met het overkoepelend WMS en zorgt voor het complete beheer binnen de liftenzone.e Verder is het voor de medewerkers aangenaam dat de plateaus uit de kast schuiven, zodat ze zich nooit over lades in de kast zelf hoeven te buigen. De medewerkers werken er ook zeer ergonomisch, aangezien goederen op de ideale hoogte worden aangeboden. Een ander voordeel van de Modula-liften is dat de goederen stofvrij worden opgeslagen.”
Om de loop- en rijafstanden op de magazijnvloer te beperken, werd gekozen voor een uitgebreid conveyorsysteem van Pacoma Systems, dat de verschillende zones met elkaar verbindt. Zowel de voorraadbakken voor de herbevoorrading als de orderbakken lopen langs dezelfde conveyor om in de juiste zone uitgesluisd te worden. Daarbij lopen de in- en outboundprocessen dwars door elkaar heen.
Toch worden er heel weinig fouten gemaakt dankzij de aansturing via het WMS en de waterdichte pickmethoden. Zo wijst bij de verticale liften een laser aan uit welk vakje de medewerker moet picken. Daarnaast ziet de medewerker de naam van de te picken artikelen op een ledstrip boven de liftplateaus verschijnen. Een pick-to-lightsysteem tegenover de liften zorgt ervoor dat de medewerker de items ook steeds in de juiste orderbak legt.
“Bij de legbordstellingen zorgt voicepicking ervoor dat er nauwelijks fouten worden gemaakt. De voorraad- en orderbakken hebben ook een andere markering, waardoor het meteen duidelijk is om welk type bak het gaat. De medewerkers moeten dus al een erg slechte nacht gehad hebben om nog fouten te maken”, lacht Erik Gies.
Gefaseerde verhuizing
De eerste stap na de inrichting van het magazijn was de verhuizing van de goederen van de vestiging in Zwolle. E. Gies: “In september 2017 waren we daarmee klaar. Hoewel we al een paar testen hadden uitgevoerd, was de opstart best pittig. De maandag nadat alle goederen waren verhuisd, zijn we beginnen uitleveren. Dat was wennen, aangezien we voordien totaal niet geautomatiseerd werkten. Een WMS, de moderne material handling systemen, het was allemaal nieuw voor ons.”
De stapsgewijze verhuizing van de voorraad van de andere vestigingen is nog steeds aan de gang. Intussen zijn – naast de voorraden van Zwolle – ook die van Veenendaal, Emmen, Almere, Tiel en Sneek in het nieuwe distributiecentrum ondergebracht. Dit jaar volgt nog het zeer grote volume van Deventer, waardoor er in één klap twintig procent orderregels zullen bijkomen.
Volgend jaar gaat het verder met Groningen en de laatste kleinere vestigingen. “Per vestiging gaat het om een stevig volume van artikelen. Bovendien hebben overal wel een aantal specifieke producten liggen, die we elders niet hebben”, vertelt Erik Gies. “Deventer is bijvoorbeeld sterk in bevestigingstechnieken en bijbehorende services. Voordat we al die artikelen en services hier in huis halen, moeten we goed nadenken over hoe we die het best kunnen opvangen. Producten die nieuw zijn voor het centrale logistiek centrum moeten we ook eerst meten om te weten in welke locaties ze terecht kunnen. Voordat een vestiging zijn voorraad op ons loslaat, zorgen we dan ook voor een overbezetting qua medewerkers om de volumes zeker op te kunnen vangen. In totaal werken we in Zwolle nu met achttien medewerkers in het logistiek centrum, maar er komen stapsgewijs mensen bij. Uiteraard kunnen we dat aantal dankzij de automatisering wel beperken.”
Vrij snel nadat het logistiek gebouw in gebruik is genomen, ging Bus Industrial Tools samen met Pacoma Systems en Vanas Engineering aan tafel zitten om na te denken over hoe de operaties er over een paar jaar uit zullen zien. Daarbij werd rekening gehouden met het extra volume na alle verhuizingen en de verwachte groei.
E. Gies: “Een van de knelpunten die we zagen, was dat het in- en outboundproces vrij dicht bij elkaar lagen. Bij verdere groei zou dat tot problemen kunnen leiden. Daarom hebben we beslist om boven de stellingen meteen een mezzanine met twee liften voor bakken en een extra stuk rollenbaan te installeren. Op die manier konden we de inbound naar boven brengen, terwijl we de zes verpakkingsstraten en de eindcontrole beneden hebben gelaten. Ook die installatie hebben we in het weekend op punt gezet, zodat we op maandag de knop konden omdraaien. Dat was opnieuw spannend, maar het is ons met de steun van onze partners toch weer gelukt.”
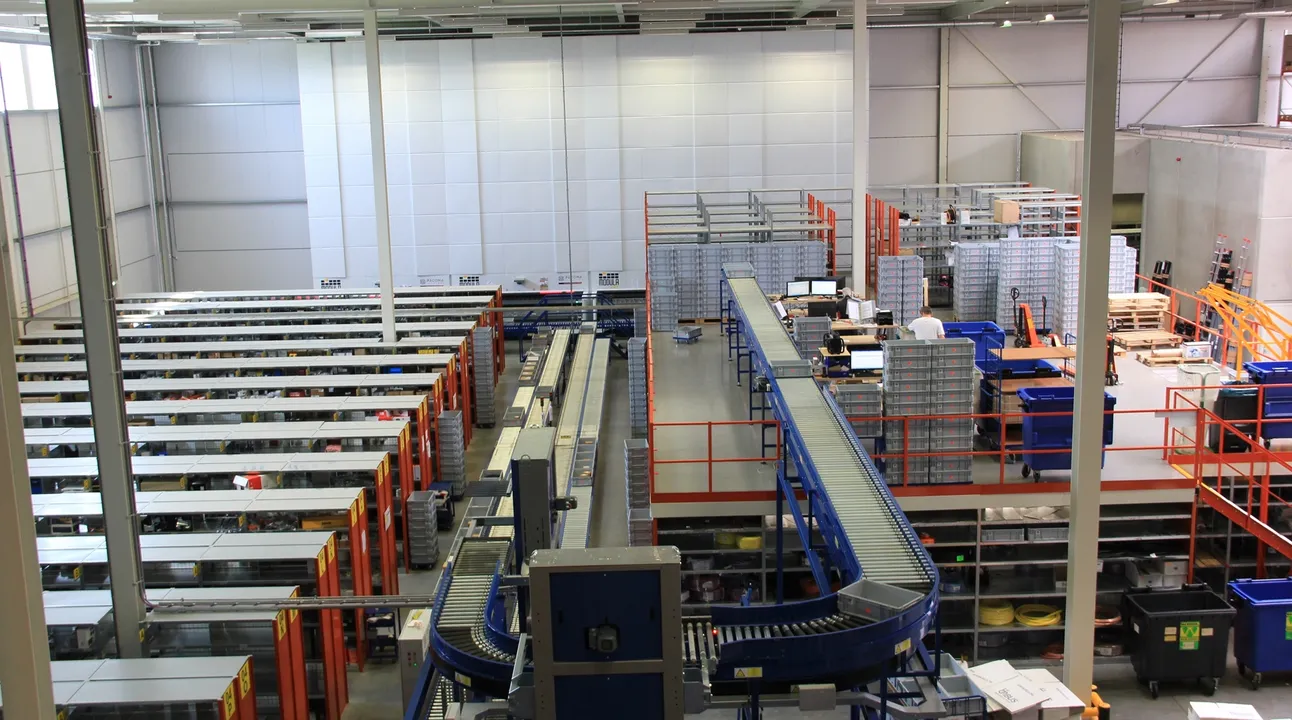
Positieve tussenbalans
De eerste stap na de inrichting van het magazijn was de verhuizing van de goederen van de vestiging in Zwolle. E. Gies: “In september 2017 waren we daarmee klaar. Hoewel we al een paar testen hadden uitgevoerd, was de opstart best pittig. De maandag nadat alle goederen waren verhuisd, zijn we beginnen uitleveren. Dat was wennen, aangezien we voordien totaal niet geautomatiseerd werkten. Een WMS, de moderne material handling systemen, het was allemaal nieuw voor ons.”
De stapsgewijze verhuizing van de voorraad van de andere vestigingen is nog steeds aan de gang. Intussen zijn – naast de voorraden van Zwolle – ook die van Veenendaal, Emmen, Almere, Tiel en Sneek in het nieuwe distributiecentrum ondergebracht. Dit jaar volgt nog het zeer grote volume van Deventer, waardoor er in één klap twintig procent orderregels zullen bijkomen.
Volgend jaar gaat het verder met Groningen en de laatste kleinere vestigingen. “Per vestiging gaat het om een stevig volume van artikelen. Bovendien hebben overal wel een aantal specifieke producten liggen, die we elders niet hebben”, vertelt Erik Gies. “Deventer is bijvoorbeeld sterk in bevestigingstechnieken en bijbehorende services. Voordat we al die artikelen en services hier in huis halen, moeten we goed nadenken over hoe we die het best kunnen opvangen. Producten die nieuw zijn voor het centrale logistiek centrum moeten we ook eerst meten om te weten in welke locaties ze terecht kunnen. Voordat een vestiging zijn voorraad op ons loslaat, zorgen we dan ook voor een overbezetting qua medewerkers om de volumes zeker op te kunnen vangen. In totaal werken we in Zwolle nu met achttien medewerkers in het logistiek centrum, maar er komen stapsgewijs mensen bij. Uiteraard kunnen we dat aantal dankzij de automatisering wel beperken.”
Vrij snel nadat het logistiek gebouw in gebruik is genomen, ging Bus Industrial Tools samen met Pacoma Systems en Vanas Engineering aan tafel zitten om na te denken over hoe de operaties er over een paar jaar uit zullen zien. Daarbij werd rekening gehouden met het extra volume na alle verhuizingen en de verwachte groei.
E. Gies: “Een van de knelpunten die we zagen, was dat het in- en outboundproces vrij dicht bij elkaar lagen. Bij verdere groei zou dat tot problemen kunnen leiden. Daarom hebben we beslist om boven de stellingen meteen een mezzanine met twee liften voor bakken en een extra stuk rollenbaan te installeren. Op die manier konden we de inbound naar boven brengen, terwijl we de zes verpakkingsstraten en de eindcontrole beneden hebben gelaten. Ook die installatie hebben we in het weekend op punt gezet, zodat we op maandag de knop konden omdraaien. Dat was opnieuw spannend, maar het is ons met de steun van onze partners toch weer gelukt.”
Denkpistes voor de toekomst
Ook in de toekomst is er nog ruimte voor verdere optimalisering. “Zo hebben we een programma opgezet om de productiviteit en de kwaliteit van onze totaalpakketten nog te verbeteren. Ook zijn we aan het onderzoeken of we niet beter kunnen omgaan met onze ‘ugly’s, zoals banken, kasten en kruiwagens. Zo zit hier een leverancier van ladders om de hoek. Die verscheept zijn artikelen wereldwijd, dus wellicht kunnen ze ook rechtstreeks aan onze klanten in Nederland leveren. Producten rechtstreeks in de verzenddoos picken is ook iets waar we uiteindelijk naartoe willen evolueren”, denkt Erik Gies luidop na.
“Verder hebben we bij de inrichting van ons magazijn weliswaar al rekening gehouden met de groei, maar dat neemt niet weg dat we vroeg of laat misschien toch zullen moeten uitbreiden. We hebben ruimte om nog enkele verticale liften naast het huidige systeem te plaatsen, mocht dat opportuun zijn. Ook tegenover de liften hebben we bij de fundering rekening gehouden met de komst van extra liften. Hoe de toekomst zal evolueren is uiteraard koffiedik kijken, maar het is fijn te weten dat we hier de ruimte en de mogelijkheden hebben om met een gerust hart verder te kunnen groeien.”