Slimme digitalisering maakt het verschil
Portals helpen Duracell bij informatiedoorstroming

Duracell in Aarschot start met een nieuw elan nadat het is overgenomen door de investeringsmaatschappij Berkshire Hathaway van Warren Buffett. De batterijenfabriek beschikt over een investeringsbudget van 50 miljoen euro om vernieuwingen en uitbreidingen door te voeren. Tegelijk loopt er een programma om efficiëntiewinst en kostenbesparing te realiseren ter hoogte van 650.000 euro per jaar. Centraal in dat project staat de introductie van ‘portals’ om informatie uit verschillende systemen naadloos naar de operatoren en managers te brengen. Daarnaast wil Duracell ook ‘machine learning’ inzetten om de kwaliteit van de batterijen nog verder op te drijven.
De fabriek van Duracell in Aarschot moet concurreren met fabrieken in Azië, niet alleen van andere batterijmerken, maar ook van Duracell zelf. Momenteel komen de meeste alkalinebatterijen uit China, Thailand of Maleisië. De laatste acht jaar hebben de meeste concurrenten nog meer productie naar Azië overgebracht. Duracell zelf zal trouwens nog een fabriek in de VS sluiten en de productie naar Azië overhevelen. In Amerika blijven er dan nog twee fabrieken over. De kwaliteit en de kosten van de Aziatische productie blijken erg goed en de fabrieken daar bepalen nu de standaard die ook de Belgische fabriek moet halen. De Duracell-fabriek in het Chinese Dong Guan presteert intussen het beste van de groep.
Stefaan Boterberg, plant director Duracell Aarschot: “De ‘landed cost’ van batterijen die in de Aziatische fabrieken geproduceerd zijn en in Europa worden verkocht, ligt nu al lager dan die van de Belgische fabriek. Wij zijn de enige fabriek in Europa van de groep en werken dan ook in de eerste plaats voor de Europese markt. In de voorbije jaren hebben wij het prijsverschil met Azië al naar beneden kunnen halen en nu hebben we een concreet plan om dat verschil tegen 2020 volledig weg te werken.”
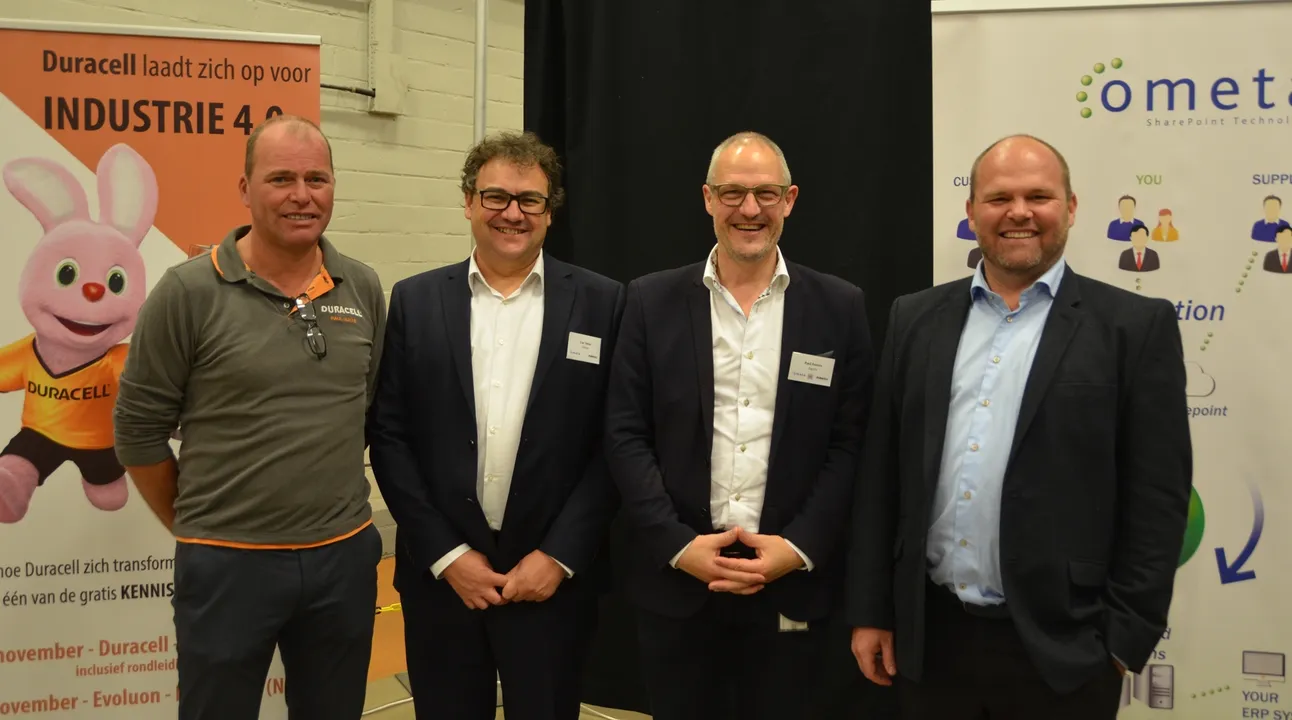
Administratie op de werkvloer
Stefaan Boterberg wijst erop dat de fabriek in Aarschot bekend staat om de hoogste kwaliteit binnen de groep. Toch kan dat het prijsverschil niet compenseren. “Het is niet zo eenvoudig geweest om met een strategie te komen”, geeft hij toe. “We kunnen toch niet hopen dat een stijgende Chinese inflatie het prijsverschil zal compenseren? En automatiseren en outsourcen doen de Chinese fabrieken evenveel of zelfs meer dan wij. Met lean manufacturing kunnen we het ook niet halen. Die methode past trouwens veel beter bij de Aziatische cultuur dan bij de onze, want de Chinese operatoren beginnen er gewoon mee zonder er eerst lang over te discussiëren. We moesten dus iets anders vinden om het verschil te maken.”
Duracell wil met een slimme digitalisering het verschil maken ten opzichte van de concurrentie binnen en buiten de groep. “We hebben vastgesteld dat we zeer veel tijd besteden aan administratie op de werkvloer”, aldus Stefaan Boterberg. “Al te lang zijn we ervan uit gegaan dat door SAP te gebruiken we onze processen volledig onder controle hadden en dat alles gedigitaliseerd zou zijn. In de praktijk stellen we vast dat veel medewerkers haast niets anders doen dan data overzetten van SAP naar Excel. We zien zelfs dat de echte topmensen in het bedrijfsleven nu diegene zijn die de beste rekenbladen maken en veel macro’s gebruiken. Tegelijk moeten we durven toegeven dat ook de systemen om kwaliteit te verbeteren en productiviteit te verhogen een stuk administratie met zich meebrengen en daardoor net het omgekeerde effect hebben. Om die reden hebben we nu drastische stappen gezet om de administratie op de werkvloer te verminderen.”
Informatie bundelen op één platform
Duracell besliste ook zijn deuren open te gooien en op zoek te gaan naar partners om die nieuwe doelstellingen te realiseren. Daarbij was het wel de bedoeling de bestaande systemen zoveel mogelijk te behouden, maar ze op een andere manier te gebruiken. Zo gebruikt Duracell intussen Office 365 en SharePoint als standaard binnen de groep. Het bedrijf riep naast de steun vanuit het Amerikaanse hoofdkwartier onder andere de hulp in van Devoteam als digitale transformatiepartner en Ometa omwille van zijn innovatieve technologie.
Arnold De Ploey, digital workplace consultant bij Devoteam: “Duracell wil stap voor stap bouwen aan een digitaal platform waar alle gegevens vanop de productiesite in real time samenkomen met informatie over de productie, de planning, het onderhoud en de opslag van de batterijen. Om daarin te slagen is ook de rol van Ometa erg belangrijk. Dat bedrijf biedt een uniek integratieplatform waarmee bedrijfsapplicaties, zoals ERP-systemen en productiesystemen gekoppeld kunnen worden aan portals en contentmanagementplatformen zoals Microsoft SharePoint.”
Bedenker van dat Ometa-framework is Luc Deleu. “Met het framework is het mogelijk de silo’s van de departementen te overstijgen en een echte samenwerking te creëren op basis van gedeelde informatie”, weet hij. “Klassiek werken bedrijven met afdelingen die vaak aparte IT-systemen hebben en waartoe andere betrokkenen geen toegang hebben. Dat maakt dat bij elke stap in het proces de medewerkers zelf voor de schakel tussen de afdelingen moeten zorgen. Met het framework wordt het mogelijk gemeenschappelijke informatieportalen te bouwen op basis van gegevens uit al die bestaande systemen, maar zodanig dat alle betrokkenen de informatie kunnen zien. We creëren dus een piramide met onderaan alle mogelijke bedrijfssystemen van plc’s tot ERP-systemen en planningsystemen, maar mensen krijgen nu zicht op het geheel van de informatie. Als iedereen die data ziet, kan iedereen meteen reageren wanneer er actie wordt gevraagd. Op die manier brengen we snelheid in de processen. In dat opzicht is de technologie heel vergelijkbaar met wat Napster vroeger deed: muziekbestanden op pc’s verspreid over de hele wereld werden toegankelijk voor iedereen die over de juiste software beschikte.”
Paul Nuyts, capability leader bij Duracell Aarschot: “We hadden een echte oplossing nodig voor dit reële probleem. Uit onze analyses van de bestaande situatie bleek dat we erg steunden op het doorschuiven van papieren om onze productie en de aanverwante processen te stroomlijnen. We dachten dat we hadden gedigitaliseerd, maar het was niet meer dan papier op glas. Volgens onze schattingen hadden we meer dan 20.000 werkuren besteed aan die schijndigitalisering en ging het daarbij om meer dan een miljoen euro aan verspilde energie. Daarbovenop kwamen nog de kosten voor menselijke fouten die gelinkt zijn aan papieren processen. Vanuit die vaststelling hebben we besloten een echte digitalisering te realiseren, waarbij we de IT-systemen onderling willen connecteren en uiteindelijk met machines verbinden. Daarbij hebben we ook de doelstelling geformuleerd om op drie jaar tijd 650.000 euro aan echte besparingen te realiseren.”
Daarvoor was het wel nodig de bestaande processen eerst grondig te bekijken en waar nodig te vereenvoudigen. Duracell wilde geen inefficiënte processen digitaliseren, eerst was een schoonmaak nodig. De tweede stap bestond erin de belangrijke IT-systemen in huis met elkaar te verbinden: ERP, MES, WMS en andere, zodat niet alleen managers maar ook operatoren op de fabrieksvloer toegang kregen tot realtime gegevens uit al die toepassingen.
Duracell besliste dat via portals te realiseren, maar dan zodanig dat ze niet alleen als dashboard worden gebruikt, maar dat er ook informatie kan worden toegevoegd.
P. Nuyts: “Bedoeling is dat informatie voor alle operatoren altijd beschikbaar is, op het juiste moment, in het juiste formaat en aangepast aan de rol die ze vervullen. De basis van dat alles is een documentmanagementsysteem gebaseerd op SharePoint. Daardoor werden de file servers per afdeling afgeschaft en vervangen door documenten die onderling met elkaar zijn verbonden en gekoppeld zijn aan taken. De overgang zal leiden tot de afschaffing van 80% van de meer dan 800.000 documenten.”
De eerste portals zijn nu geïmplementeerd op een assemblagelijn voor de AA-batterijen. Die bevatten al een aantal toepassingen zoals het overzicht van de productieorders, de rapporten over uitval, procedures voor machineomzettingen met interactieve takenlijsten, enzovoort. Daarnaast is er heel wat aandacht besteed aan de digitale kwaliteitsborden. De belangrijke informatie over de voorbije productie wordt automatisch aangevuld in een digitaal scherm. Daar hoeven de kwaliteitsmensen dus geen tijd meer in te stoppen. Alle informatie over productieplanning, productiehoeveelheden, afvalpercentages, onderhoud, veiligheids- en kwaliteitscontrole, die voorheen op verschillende plaatsen manueel verwerkt werd, stroomt straks meteen en automatisch door naar SharePoint.
Als ze daar eenmaal in geslaagd zijn, kan de werking van de productieteams bij Duracell verder worden gedigitaliseerd.
A. De Ploey: “Computers en tablets worden het vertrek- en het eindpunt in de dagelijkse werking van arbeiders. Zij krijgen via schermen de taken toegewezen die ze moeten uitvoeren. Staan hun taken in het rood, dan betekent dit dat ze die eerst moeten uitvoeren. Als ze klaar zijn, vinken ze hun taak af en verdwijnt die van het scherm. Dat wordt dan weer automatisch verwerkt op SharePoint in de vorm van dashboards die de status van taken en de KPI’s visueel weergeven. Zo beschikt Duracell altijd over de meest recente informatie.”
Machine learning
Daarnaast hebben de productieverantwoordelijken nog een doelstelling. Ook na jaren van kwaliteitsinitiatieven blijven er mogelijkheden om de productie verder te verbeteren. Dat doet geen afbreuk aan de volgehouden inspanningen uit het verleden.
P. Nuyts: “Zeven jaar geleden stond de productie om de haverklap stil. We hebben die honderden stops per dag kunnen terugbrengen naar een twintigtal. We hebben enorme stappen vooruitgezet, maar dat werk is nooit gedaan. Het kan altijd nog beter.”
S. Boterberg: “Nog elke dag keuren we 50.000 batterijen af omwille van kwaliteitsproblemen. We zijn dan wel de fabriek die de beste kwaliteit aflevert binnen de groep, dat blijft toch een groot volume. Die batterijen hebben het hele productieproces doorlopen en we hebben er dan ook materiaal en tijd aan besteed. Als we erin slagen eventuele problemen vroeger te ontdekken, dan kunnen we ook de productiekosten doen dalen. Om dat te doen, willen we diepgaande analyses maken om dan via machine learning de onderliggende oorzaken te vinden. Daarvoor moeten we nog meer gegevens verzamelen tijdens het productieproces. We zijn van plan voor elke batterij 30 kritische datapunten te registreren. Op termijn kan dat zelfs uitgroeien tot 100.”
Op basis van een beperkte dataset is een eerste poging ondernomen om correlaties tussen de metingen te ontdekken. “Het komt erop neer dat we de historische data nemen die gelinkt zijn aan de afgekeurde batterijen. Als we precies weten welke fenomenen bij de productie van een mislukte serie optreden, kunnen we wellicht ook voorspellen wanneer zich dat op een lopende productie zou kunnen voordoen. Dat is intussen inderdaad ook gelukt”, vertelt Paul Nuyts.
Duracell heeft één deelproces onder de loep genomen, namelijk de productie van het materiaal van de anode. Dat is een zinkpasta waaraan een aantal additieven worden toegevoegd om de capaciteit van de batterijen te verbeteren. Die pasta ontstaat in een mengproces en daarvan werden twaalf parameters geselecteerd zoals de vochtigheidsgraad, temperatuur, de snelheid van de mengschoepen, enzovoort. Duracell en zijn partners zijn er intussen in geslaagd de oude labresultaten te voorspellen door gebruik te maken van de bestaande data en ze te analyseren met Python Machine Learning.
P. Nuyts: “Nu we weten dat we labresultaten kunnen voorspellen, moeten we in de nabije toekomst de volgende stappen zetten. Op korte termijn hoeven we niet meer naar het lab om een batch goed of af te keuren. Dus kunnen we nu laboratoriumtijd vrijmaken om bijkomende analyses uit te voeren en verbeteringen voor te stellen. Maar op langere termijn zullen we het proces in realtime kunnen bijsturen om te voorkomen dat het mislukt. Daarna willen we die manier van werken in veel meer processen invoeren.”
Digitale tweeling
Een belangrijk concept voor die toekomstige evolutie is de ‘digital twin’. Duracell wil van elke batterij die het produceert – en dat zijn er 5 miljoen per dag – een digitale tweeling maken. Een gedigitaliseerde versie van de echte batterij bestaande uit een hele resem kritische parameters die bepalend kunnen zijn voor de kwaliteit van het product. Bedoeling is die parameters in realtime op te volgen tijdens de productie. Op die manier kunnen de lijnverantwoordelijken dankzij machine learning voorspellen wanneer de productie niet goed is. Zo kunnen ze ingrijpen om het proces te verbeteren of indien nodig de batterij uit het proces te halen.
P. Nuyts: “Dat vergt een heel andere manier van werken. Nu is de kwaliteitscontrole nog volledig gebaseerd op controles achteraf. Straks willen we een controle op elke batterij voor elke kritische processtap. Het afvullen van de batterijcellen is bijvoorbeeld een heel gevoelig proces waarbij de hoeveelheid zinkpasta cruciaal is. In de toekomst zullen we dat voor elk batterij meten. Ook de metalen cellen zullen we straks met een laserscanner 100% op beschadigingen controleren.”