De wondere wereld van warehouse robotics
Prof. René de Koster schetst de mogelijkheden binnen het magazijn
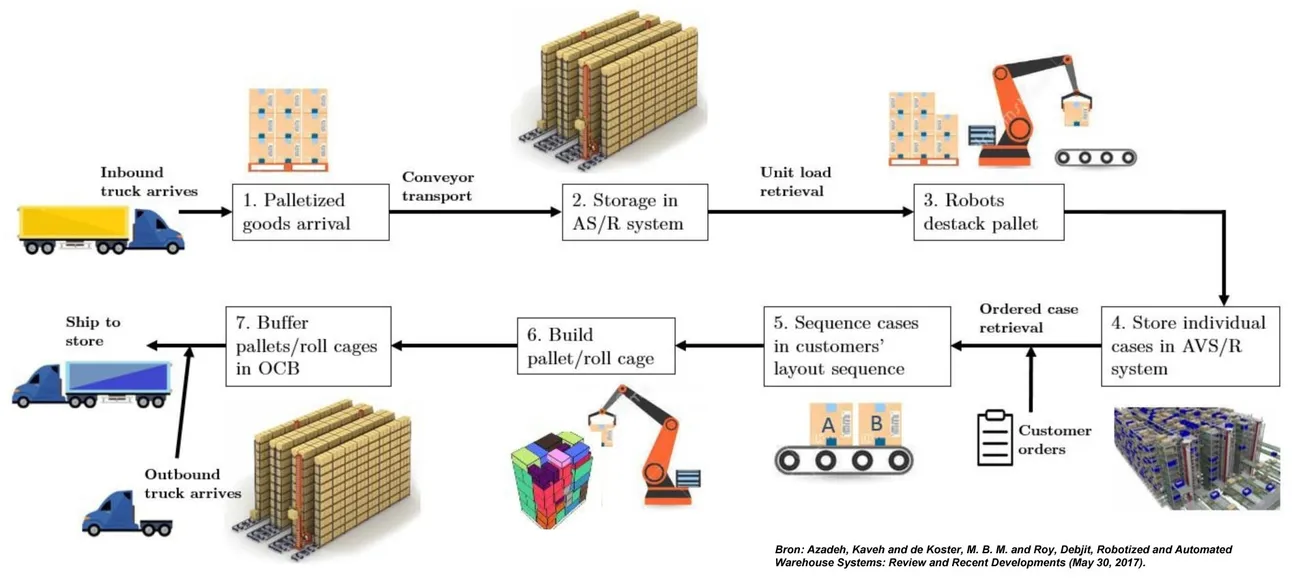
In steeds meer omgevingen zien we robots opduiken. Dat is binnen magazijnen niet anders. Leveranciers van material handling systemen pikken gretig in op deze trend. Een goede zaak, al is het niet eenvoudig om het potentieel van elk systeem goed in te schatten. Omdat de ene robot de andere niet is, geeft professor René de Koster, professor of Logistics & Operations Management aan de Erasmus Universiteit Rotterdam, een handig overzicht van de diverse types robots die de efficiëntie binnen magazijnomgevingen kunnen verbeteren.
Bij het begrip ‘warehouse robotics’ zullen velen spontaan denken aan de tot de verbeelding sprekende pickrobot. Warehouse robotics dekt evenwel een veel bredere lading. Die splitst René de Koster op in verschillende categorieën op basis van hun functie binnen het magazijn. Binnen de meest ingeburgerde categorieën vinden we intussen al een waaier aan variëteiten terug, andere staan nog in hun kinderschoenen.
1. Shuttlesystemen: robots met maturiteit
Populair binnen magazijnen zijn tegenwoordig de zogenaamde shuttlesystemen. De snelle opmars van e-commerce werkt de adoptie van dergelijke systemen – met een hoge flexibiliteit als gunstige eigenschap – in de hand.
Binnen zulke systemen is de robot de shuttle die autonoom binnen de stellingen meestal bakken transporteert. Doorgaans bewegen de shuttles zich zeer snel horizontaal op het X- en Y-niveau, terwijl liften zorgen voor de verticale beweging. Als de bak de lift verlaat, gaat die in de regel via een conveyor naar het pickstation. In sommige gevallen worden shuttles ook ingezet om pallets te behandelen.
Shuttles in combinatie met liften
Intussen bieden heel wat leveranciers van material handling systemen shuttlesystemen aan. We kunnen gerust stellen dat deze robottechnologie al matuur is. Vandaag vinden we ook al een aantal varianten onder de shuttlesystemen terug. Zo kunnen de shuttles in bepaalde gevallen van gang wisselen en/of gaan ze mee met de lift naar beneden. Welke variant voor een welbepaald magazijn het meest geschikt is, zal een afweging zijn tussen de gewenste terugverdientijd, flexibiliteit en snelheid.
Binnen de groep shuttlesysteem bewegen zich ook nog een aantal andere buitenbeentjes. “Denken we maar aan het Autostore-systeem, dat Hatteland produceert”, illustreert prof. René de Koster. “In dat systeem bewegen de shuttles zich over een raster en ‘takelen’ ze als het ware de bakken uit de kanalen van een enorme kubus om ze vervolgens naar het uitslagkanaal te brengen. Aan het orderpickstation wacht een picker de bakken op en neemt het gewenste aantal artikelen uit de bak.”
“Bij dergelijke systemen is optimalisering belangrijk om het onderste uit de kan te halen. Wat betreft het Autostore-systeem, hebben we ons in het kader van een onderzoek afgevraagd of het beter is om elk kanaal met bakken van slechts één referentie te vullen (dedicated storage) of er beter bakken met verschillende referenties in opslaat (shared storage)”, vervolgt de professor. “Kanalen met maar één referentie hebben het nadeel dat je een LIFO-systeem (Last in First Out) krijgt maar er is geen tijdrovende reshuffeling vereist. Kanalen met meerdere referenties hebben dan weer het voordeel dat je minder kostbare ruimte nodig hebt, want in het ‘dedicated storage’ scenario zal niet elk kanaal altijd volledig met eenzelfde referentie kunnen worden gevuld. Uit ons onderzoek bleek dat het bijna in alle gevallen beter is om in dit systeem de referenties te mixen voor een optimale balans tussen throughput en capaciteit. Zulke zaken zijn goed om vooraf te weten als je met zo’n systeem aan de slag wil gaan.”
Driedimensionale shuttlesystemen
Daarnaast bestaan er systemen waarbij de shuttles niet enkel op de X- en Y-as, maar ook verticaal of diagonaal kunnen bewegen. Een voorbeeld zijn de driedimensionale Skypod robots van Exotec Solutions. Ook de iBot-shuttles in het PerfectPicksysteem van het Amerikaanse Opex kunnen zich zowel in de horizontale als de verticale richting bewegen. Fraunhofer IML heeft met de RackRacer dan weer een systeem ontwikkeld waarbij de shuttles zich ook diagonaal tussen de rekken kunnen bewegen. Binnen die systemen wordt dus geen gebruik gemaakt van liften.
Prof. R. de Koster: “Binnen een ander onderzoek hebben we de tweedimensionale shuttles in combinatie met een lift vergeleken met shuttlesystemen die zich zowel horizontaal als verticaal kunnen bewegen en het dus zonder lift doen. Voor diverse opslagcapaciteiten en een gegeven throughputcapaciteit hebben we de jaarlijkse kosten van de twee types systemen vergeleken. In de meeste gevallen bleken de driedimensionale systemen het voordeligst. Alleen wanneer de opslagcapaciteit en de throughput per gang extreem hoog moet zijn, komt een tweedimensionaal systeem als goedkoopste uit de bus. Een nadeel is wel dat er nog maar een paar leveranciers zijn die driedimensionale systemen aanbieden, terwijl de aanbieders van shuttles met liftsystemen niet meer op twee handen te tellen zijn. In elk geval verwacht ik binnen beide types systemen een verdere evolutie op het vlak van performantie, waardoor ze voor steeds meer magazijnen interessanter zullen worden.”
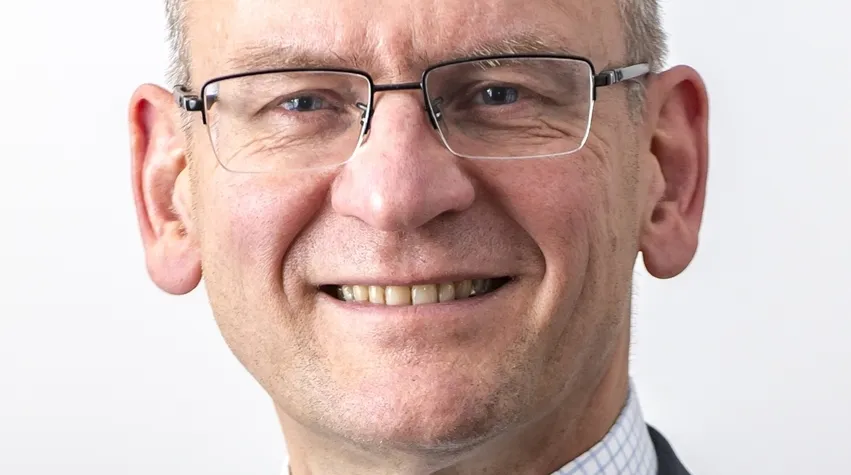
2. Shuttlegebaseerde rekken met hoge flexibiliteit
Het was leverancier Kiva die de shuttlegebaseerde rekken – ook wel Autonomous Mobile Racks (AMR’s) genoemd – binnen de warehouses introduceerde. Sinds Amazon het bedrijf in kwestie overnam, zijn deze robots exclusief eigendom van de internetgigant, die ze al in tientallen magazijnen in gebruik heeft genomen. Gelukkig hebben intussen heel wat leveranciers – zoals Grey Orange, Swisslog/Grenzebach, Scallog en Suning – soortgelijke oplossingen op de markt gebracht. Alibaba is trouwens zijn concurrent gevolgd met een vergelijkbaar systeem van Quicktron. Het achterliggende principe is dat deze robots zich onder de rekken bewegen en ze een paar centimeter optillen. Vervolgens brengen ze het rek naar het pickstation, waardoor de orderverzamelaar geen lange afstanden meer hoeft af te leggen.
Prof. R. de Koster: “Een groot voordeel van dit type robots is dat ze een hoge flexibiliteit in je magazijn garanderen. Ook voor onderzoek is dit een dankbaar type systeem, aangezien het toelaat op een heel dynamische manier een faciliteit een nieuwe lay-out te geven. Op die manier kunnen we bijvoorbeeld de ideale balans tussen werkstations voor picking en replenishment onderzoeken en dynamisch veranderen. Ik verwacht dat in de toekomst ook steeds vaker op dit type systemen zal worden ingezet in bijvoorbeeld e-commerceomgevingen die een hoge flexibiliteit vragen.”
3. Het potentieel van puzzelgebaseerde shuttlesystemen
Bij puzzelgebaseerde shuttlesystemen ligt elke lading op één shuttle. “Een mooi voorbeeld van zo’n systeem zijn geautomatiseerde parkeergarages, waarbij je je wagen bij de ingang van het systeem afzet en het systeem hem automatisch op een locatie in het systeem puzzelt”, illustreert René de Koster. “Het mooie van dit systeem is dat je geen gangen nodig hebt, maar alleen liften en shuttles. Dat maakt het systeem extreem compact. Zo’n systeem bestaat vooralsnog niet voor magazijnomgevingen, maar de software om het goed te laten werken, is er wel. Het belangrijkste nadeel van het systeem is wel dat het logischerwijze heel prijzig zal zijn, aangezien elke lading zijn eigen shuttle heeft.”
Een systeem dat bijvoorbeeld wel al actief is bij een Chinees koeriersbedrijf, zijn robots met plaats voor één lading om pakketten te sorteren. Elk exemplaar binnen het leger van zo’n 300 oranje robots kan één pakket tegelijk dragen en het naar een gat in het ‘conveyor rooster’ brengen om daar zijn lading in te werpen. Het achterliggende scansysteem zorgt ervoor dat alle pakketjes op de juiste locatie worden gelost. Er is alleen nog een medewerker nodig die de aankomende pakketten op de robot legt. Via dit futuristische systeem is het mogelijk op een zeer beperkte oppervlakte minstens 200.000 pakketten per dag – of 20.000 pakketten per uur – te sorteren. Dit robotsysteem werd ontwikkeld door het Chinese technologiebedrijf Hikvision.
4. De snelle evolutie van pickrobots
Terwijl bij de voorgaande systemen de eigenlijke picking nog steeds door medewerkers wordt gedaan, neemt de pickrobot ook dit werk uit handen van de mensen. Nadelen van pickrobots is dat ze nog meer tempo moeten krijgen om echt interessant te worden en dat ze nog steeds relatief duur zijn. Maar ook daar wordt werk van gemaakt. Een goede beeldherkenning zorgt ervoor dat de robots efficiënt de goederen kunnen grijpen. Ook die technologie wordt steeds beter.
Prof. R. de Koster: “De fabrikant Robomotive, bijvoorbeeld, staat al behoorlijk ver op het vlak van innovatieve robotvisietechnologie. Zij bieden robots die in staat zijn de juiste producten uit gemengde bakken te verzamelen, zelfs als die een verschillende zuigkracht vragen om ze op te nemen. Ze oriënteren de zuigkop ook steeds op het zwaarste punt, zodat het product er niet afvalt. Naast het vacuümsysteem is het ook mogelijk artikelen met grijpers te nemen. Die technologieën verbeteren continu, zodat de waaier en het gewicht van de goederen die die robots kunnen verzamelen steeds breder wordt. Uiteraard zal de kans groot blijven dat je niet alle goederen binnen het assortiment met een robot kunt picken.”
5. Picking met behulp van AGV’s
Een laatste categorie robots voor het magazijn bestaat uit Autonomated Guided Vehicles die de medewerker bij zijn pickactiviteiten ondersteunen. “Zo zijn er robots die automatisch de orderpicker volgen, denken we maar aan de Still iGo neo of de Crown QuickPick Remote”, illustreert René de Koster. “Op die manier hoeft de magazijnmedewerker niet iedere keer weer op en af zijn orderpicktruck te stappen. Een productiviteitswinst tot twintig procent is met deze toestellen zeker mogelijk.”
Binnen dit genre zijn er ook robots die nog meer taken van de orderpicker overnemen. De robots van de firma Locus Robotics, bijvoorbeeld, komen helemaal zelfstandig naar de orderpicker toe en tonen op hun display welke items de orderpicker in zijn bak moet leggen. Heeft de robot dat item gekregen, dan vervolgt hij zelfstandig zijn weg. Op die manier worden de loopafstanden voor de orderpicker geminimaliseerd en kan de robot ten dienste van orderpickers in verschillende zones worden gesteld. Dergelijke robots fungeren ook prima als verlengstuk van een goods-to-man-systeem, waarbij ze bijvoorbeeld aan het orderpickstation bakken automatisch naar de verzendzone kunnen brengen.
Nog een stap verder gaat de firma Vecna Robotics, die geavanceerde robotsystemen levert. De robots van dit bedrijf zijn zelfs in staat om zelf voorraadbakken uit het rek te halen en ze naar een pickrobot te brengen die de gewenste producten in de orderbak op een andere robot legt. De Toru van het Duitse Magazino kan eveneens zelfstandig dozen uit een rek halen en er bovendien meerdere tegelijk meenemen. Dat de populaire modewebschop Zalando fors in dit laatste bedrijf heeft geïnvesteerd, bewijst wel dat ook de groten van deze aarde in deze geavanceerde technologie geloven. De mobiele pickrobot Swift van IAM Robotics kan zelfs afzonderlijke producten rechtstreeks uit het rek picken. Uiteraard zit aan dergelijke hoogtechnologische robots wel nog een hoog prijskaartje vast.
De bijdrage van robots aan het compleet geautomatiseerde warehouse
Dat de combinatie van robotiserings- en andere automatiseringstechnologieën een steeds groter potentieel krijgt, lijdt volgens prof. René de Koster geen twijfel. “Nu al zijn er magazijnen die nagenoeg volledig geautomatiseerd zijn. Binnen Europa zijn er momenteel een veertigtal compleet geautomatiseerde magazijnen. Naarmate de robot- en automatiseringstechnologieën verbeteren, zal die trend alleen maar versterken.”
Prof. René de Koster geeft een voorbeeld van zo’n volledig geautomatiseerd retailmagazijn (zie figuur 1) waar dozen voor winkels worden verzameld. Leveranciers lossen er hun trucks en voeden de check-in conveyors met homogene pallets. Vervolgens worden de pallets opgeslagen in een Automated Storage & Retrieval systeem. Als een bepaald product nodig is, wordt de pallet automatisch ontstapeld. De losse dozen worden dan op trays geplaatst met het oog op een gemakkelijke manipulatie en in een miniload of shuttlesysteem opgeslagen. Als de orders van de winkels binnenkomen, worden de gewenste dozen verzameld en via palletiseermachines op pallets of in rolcontainers verzameld. Daarbij wordt rekening gehouden met de locatie van de producten in de winkel, wat het werk op de winkelvloer vereenvoudigt. Vervolgens wachten de pallets in een orderconsolidatiebuffer – vaak is dat een Automated Storage & Retrieval systeem – tot de juiste truck aandockt. Tot slot worden ze automatisch opgehaald en geladen in de volgorde van de stops op het traject van de truck. Los van de technici die nodig zijn om zo’n warehouse draaiende te houden, is hier geen manuele arbeid meer vereist.
Maar het spreekt voor zich dat het aandeel gedeeltelijk geautomatiseerde magazijnen groter zal blijven dan de volautomatische sites. Vooral dit type magazijnen belooft de komende jaren toe te nemen. Volgens Buck Consultants International zijn er in de periode 2012-2016 63 grote nieuwe magazijnen in Nederland gebouwd waar robottechnologieën worden ingezet. Hoewel er nog geen nieuwe cijfers beschikbaar zijn, lijdt het geen twijfel dat daar, dankzij de snelle evoluties van het voorbije anderhalf jaar, nog heel wat sterk geautomatiseerde magazijnen zijn bijgekomen. Zeker in de nieuwe, grotere e-commercemagazijnen wordt automatisering meestal systematisch overwogen.
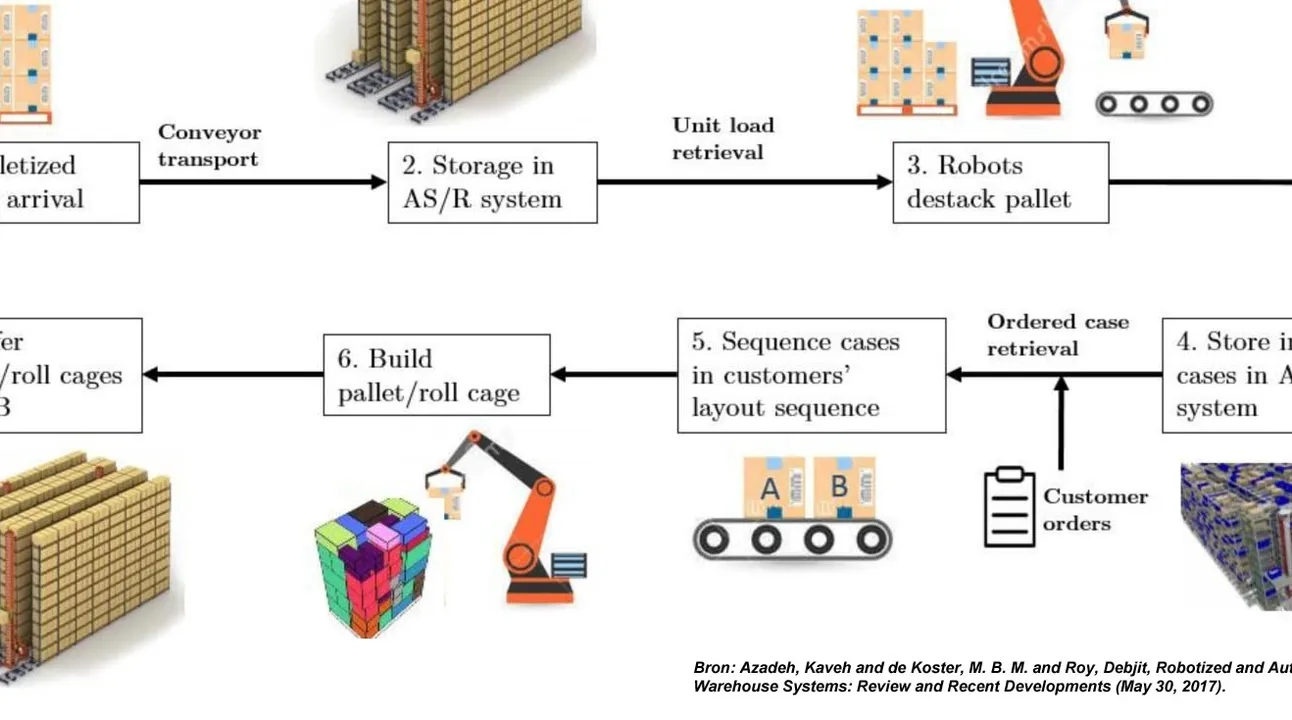
Innovaties vragen verder onderzoek
Als we terugblikken op de genoemde categorieën, dan mag het duidelijk zijn dat er momenteel al heel veel verschillende robotsystemen voor het magazijn bestaan en dat er druk aan de verfijning en verdere ontwikkeling wordt gewerkt. Dat de systemen in de toekomst steeds interessanter zullen worden, daarover bestaat geen twijfel. Maar hoe interessant ze vandaag precies zijn, is toch nog vaak nattevingerwerk.
“Zeker bij de nieuwste technologieën is het niet eenvoudig om de waarde ervan goed in te schatten. Wat ons betreft zijn dergelijke systemen voer voor verder onderzoek. Wat is de ideale verdeling tussen taken voor de robot en de mens? Hoe flexibel zijn dergelijke systemen in piekperiodes? Hoe kun je ze goed integreren in supply chain concepten? Hoe selecteer je het beste systeem voor jouw operaties? Het zijn vragen waar wij ons in de toekomst als onderzoekers graag over willen buigen”, besluit prof. René de Koster.